Forming, pressing and laminating with vacuum are popular processes in many branches of industry and in manufacturing technology. These processes are used to join a large variety of materials together or form them into a specific mold.
For forming, it is important that a clearly defined vacuum is used to bring the material into the mold. An established process and one that is used for many products is thermoforming, which is used to shape plastic foils. For this process, plastic foils are heated to soften them. Vacuum is applied through the mould. This pulls the foil, which has been softened by the heating process, into the mold. Once the foil has cooled down, it holds the shape of the mold. This method can be used to create packaging for food products and other commodities, and even preformed plastic forms for garden ponds.
.jpg)
Pressing with vacuum is used in the wood industry, for example, when several layers of wood are glued together and mechanical pressing cannot be used because of the geometric shape. Vacuum can also be used to attach veneers or to fix synthetics to wooden profiles, for example onto kitchen fronts.
.jpg)
Laminating under vacuum is a process that is used to join different layers of materials together, and one that is commonly used in semiconductors and the electronics industries. Solar modules, flat screens and smartphone displays are created in this way.
Which Hokaido vacuum solutions are especially suitable for forming, pressing and laminating applications?
State-of-the-art RH series rotary vane vacuum pumps have been proven in forming applications with many years of successful operation.
The energy-efficient RC claw vacuum pumps can be used for pressing when low vacuum is acceptable, in producing furniture for example. If higher vacuums are required, RH rotary vane vacuum pumps are the first choice.
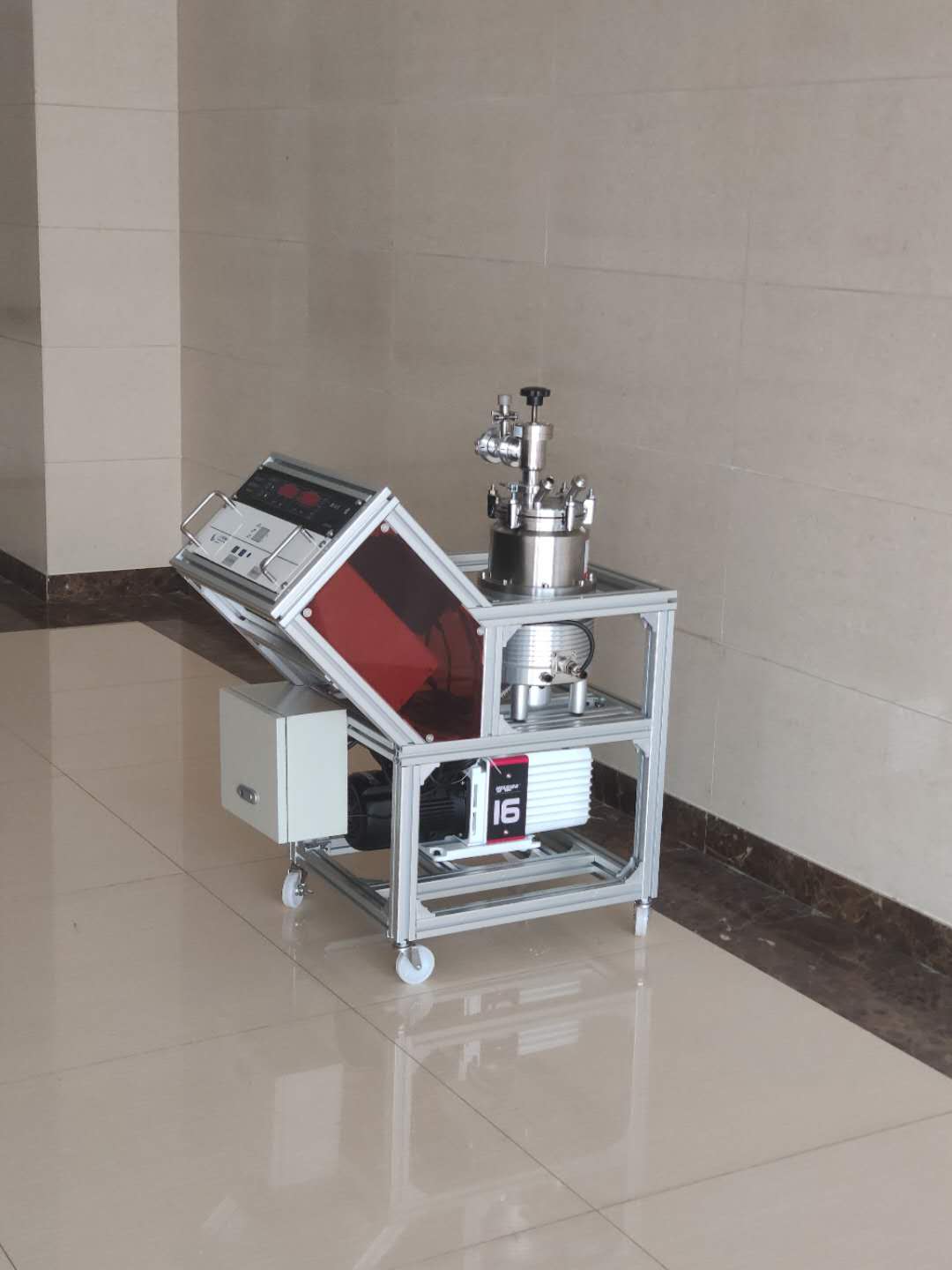
2RH-C/2RH-D series double-stage oil vacuum pumps are the preferred vacuum pumps for laminating processes in the production of solar modules, flat screens and smartphone displays because they can discharge leaking gases and vapours without interference.